DuraLite for Aerospace
Few industries rely on polyurethane as heavily as the aerospace industry, and it’s easy to understand why. Polyurethane can handle environments that most other materials cannot, owing largely to the versatility it shows during fabrication. Polyurethane can be fabricated in a number of forms, allowing it to exhibit an impressive range of properties. These properties make it a mainstay in oil and gas pipelines, construction sites, manufacturing plants and, most relevantly, aircraft and spacecraft.
Polyurethane foam is a marvel of engineering, and is used extensively in aircraft and spacecraft. In typical passenger craft, it’s common for seating to be padded with polyurethane foam. In addition to the seating, polyurethane foam may be found in the aircraft’s insulation, its walls and ceilings, baggage compartments, and dividers between class segments and lavatories. Polyurethane foam can be found in similar capacities in military aircraft as well. In addition to providing a durable and inexpensive material for aircraft, polyurethane foam can be augmented with fluid to make it extremely airtight. By filling the tiny vesicles in the foam with fluid, it’s possible to maintain internal air pressure with little effort. Clearly, keeping air leakage to a minimum is a major priority in the aerospace industry.
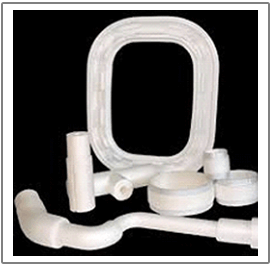
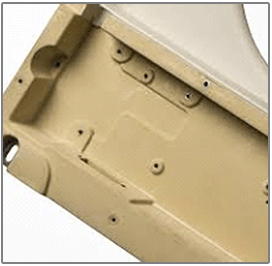
Throughout the flight process, aircraft are exposed to numerous challenges. The exterior of the craft as well as the interior are both subject to rapid and large changes in temperature. Because aerospace foam features advanced temperature and insulating properties, polyurethane can protect the aircraft as well as the passengers inside it from extreme temperature fluctuations. Aerospace foam density also helps to prevent air leakage into or out of the aircraft, helping to preserve cabin pressure. Polyurethane aerospace foam can also provide a strong sound barrier, helping to protect passengers from the high decibel levels of aircraft engines and more. Its compressive strength, ability to vary in strength for different needs, and overall inexpensiveness to produce also contribute to its wide usage in the aerospace industry.
We can supply custom-built polyurethane foam materials to original equipment manufacturers and Tier 1 and Tier 2 companies. Our custom-moulded polyurethane products and aerospace-grade rigid foam core materials are used in aircraft flight decks and interior cabins.
We can also machine and fabricate rigid foam board and flexible foam materials to demanding aerospace and military defence specification. Our materials have been engineered to satisfy the physical property and flammability requirements of the aerospace and military industries.
A Total Solutions Partner
Defex is equipped to manage all aspects of a moulded-foam part program. We can assist in part design, tool design, mould tooling manufacture, and production of parts through all phases to completion. When necessary, we will custom-formulate appropriate foam systems with all the physical properties and other attributes your project requires.
Moulding Infrastructure:
- Part/tool manufacture based on customer specifications
- Model-to-print and pattern-to-print services
- Mould tooling manufacture
- Formulating foam with full QA documentation
- Dedicated assembly room for engineered parts
- Segregated, controlled-access ITAR assembly room for military parts
- Mould development services
Testing Services:
- Flammability
- Physical Property
- Developmental
Custom Moulding,
Fabrication & Assembly Services:
- Pattern making
- Prototype design and manufacture
- Tooling
- CNC machining
- Painting
- Adhesive bonding
- Prepreg, potting and resin-infusion processes
- Tooling Board
- Prototypes
- Wingtip-Lens Transparencies
- Vacuum-forming Tools
- Mould Patterns
Applications:
- Overhead Headliners
- Assist Panels
- HUD Covers
- CD Post Pads
- Glare Shield Pads
- Kick Strips.
Core Material
- Cabin Walls and Ceilings
- Service-Class Dividers
- Galleys and Lavatories
- Sandwich Panel
- Honeycomb Edge Closeout
Gap Management
- Gap seals
- Overhead Stow Bins
- Exit Row Armrests
Flight Deck
- Overhead Headliners
- Assist Panels
- HUD Covers
- CD Post Pads
- Glare Shield Pads
- Kick Strips.
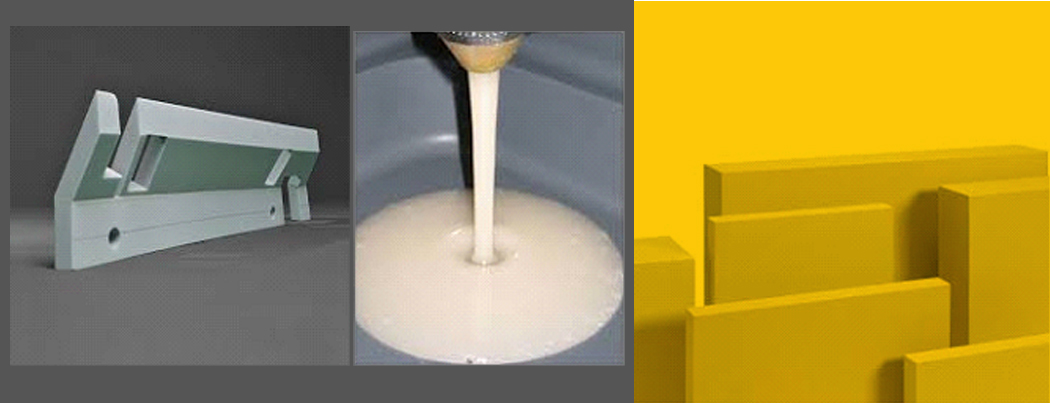
Flexible Foams – Sheet and Custom Parts
Available in multiple densities, DuraLite™versatile polyurethane flexible foams can be a staple of aircraft interiors. Certified to meet FAR 25.853 standards, our self-skinning, fire-retardant flexible foam products can be used extensively in flight deck and cabin applications. They deliver solid efficiency while absorbing energy at a consistent, controlled rate.
DuraLite Energy Absorbing Flexible Foam TI 6400 Series
DuraLite Energy Absorbing Semi-Flexible Foam TI 8000 & TI 9400 Series
DuraLite Energy Absorbing Semi-Rigid Foam TI 12400 Series
Offered in sheets, blocks and moulded parts, these products are extremely durable and resistant to environmental stresses. They are formulated to absorb significant energy while protecting payloads from high stress levels. Specific product applications include aircraft interior crash padding, and vibration dampening / cushioning for missiles and nuclear submarine launch tubes.
Rigid Foams
DuraLite rigid foam products are cost-effective, versatile, strong and durable. They are manufactured using our unique chemical formulas to be exceptionally uniform and consistent in all physical properties. DuraLite offers a wide spectrum of foam formulations, in multiple shapes and densities.
DuraLite FR-6000 FST Performance Core
This lightweight, rigid foam core satisfies fire, smoke and toxicity (FST) performance needs. Used in conjunction with other materials, it contributes to both aesthetics and safety. This product complies with the Ohio State University (OSU) 65/65 heat release standard, FAA flame and smoke regulations, and aircraft manufacturer toxicity requirements.
FST foam offers aerospace designers and manufacturers a lightweight, cost-effective option for a wide variety of sandwich core panels that require the additional fire safety properties for heat release, fire, smoke density, and toxicity (FST). The FST and Ohio State University (OSU) heat release designation refers to a series of performance requirements for materials used in aircraft interiors. In most cases, these requirements apply to large ceiling and wall panels or structures that cover large surface areas within the aircraft.